Liam Hess travels to Santoni’s headquarters in Corridonia, Italy, and discovers a brand where traditional technique meets modern thinking
- TextLiam Hess
What makes a perfect shoe? It’s a question that Giuseppe Santoni – CEO of the shoemaking house Santoni, and son of its founder, Andrea – has been asking himself for many decades. “I see it as a fusion of the young and the old,” he says, over coffee on a winter morning at the company’s Italian headquarters. “None of our designers are more than 40 years old, but if you look at the artisans making the shoes, many of them have white hair. We match these two cultures: young people who want to innovate and try new things, and expert craftsmanship that can keep the more traditional qualities alive.”
While the company today may be significantly larger than its first iteration in the early 1970s, when it was based out of the garage of their family home, every shoe is still entirely crafted and shipped from its headquarters in the town of Corridonia in the heart of Italy’s Marche region. The surrounding area is well known for its centuries-old tradition of artisanal shoemaking, but Santoni has come to represent its apex – and Giuseppe, leaning back in a dapper three-piece suit against the living wall of his sustainable conference room, is its perfect ambassador. It helps that he has an estimated personal collection over 450 pairs of shoes – “a room as big as this,” he says, gesturing around the space – including pairs he’s owned for over 30 years.
The building stands out within its surroundings of a typical suburban Italian town: from the outside, it appears an ultra-modern architectural monolith of steel, aluminium and glass, but its interiors reveal an open-plan space flooded with natural light, punctuated by greenery and running water. It turns out 90 per cent of the materials used during construction were recyclable, and the entire factory is powered by photovoltaic panels across its rooves, making a Santoni shoe entirely carbon-neutral.
More surprising, even, is the fact that the building was opened almost a decade ago, many years before sustainability became a central industry conversation. “We began planning an environmentally friendly building back in 2005,” Santoni remembers. “I’ve always believed that luxury is not about product, it’s a philosophy. If we stand for quality and excellence, the way we think should reflect that, too, and paying attention to the future and to the younger generation is a big responsibility for men in power when they are making decisions.”
This balance of the profoundly traditional and the cutting-edge is clear when taking a short walk around the factory. (Also, who knew there were so many moving parts to make a shoe?) While every stage of the process is either shaped by human hands – even when machines are involved, they’re guided with care and precision – the intricacies of crafting a piece of footwear quickly become apparent. Tracing, cutting, punching, stitching, assembling, and, uniquely to Santoni, hand-painting: hunched over their desks, dozens of workers apply layer upon layer of paint to achieve the brand’s signature burnished, ombré colours.
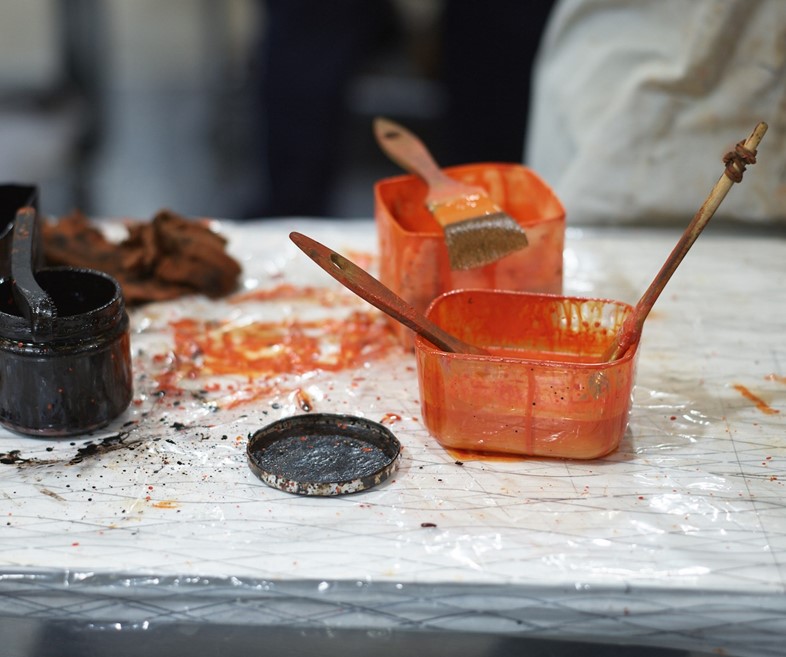
One particular piece of kit speaks to the company’s finely tuned balance of craftsmanship, tradition and radical innovation: the giant boards with projectors above them, where workers lay out sheets of leather before positioning (with the help of a computer mouse) lit-up shapes to cut from and ensure as little wastage as possible. After they navigate their way around the blemishes and select their chosen patterns, the leather gets swept over to one side and sliced with a mechanical, razor-sharp needle. “You have to think of it a bit like an Olivetti typewriter,” Santoni explains. “It’s very romantic, but it’s much easier to use Microsoft Word if you’re writing a letter and print it out. You need to be cultured to know what you’re typing, but the end result will be better with the help of a machine.”
Most extraordinary of all is the brand’s Uniqua style, launched earlier this year and retailing in the thousands – and for good reason, given the shoe is assembled from a single piece of leather, without any seams at all. For Santoni, it’s the ultimate expression of the craft he holds so dear. “Yes, it’s anti-economical,” he adds, “in the sense that if our business model was just producing Uniqua shoes, we would be out of business. But it’s about expressing the ultimate vision of what we can do.”
Santoni is keen to emphasise that he’s not just designing shoes, but creating works of beauty. So how does this all fit into his mission statement of reimagining luxury as something more soulful? “In our company, we don’t have workers, we have artists,” he says, with a very Italian mix of pride and passion. “A worker uses the hands; artisans the head and hands; while artists use the head, heart and hands.” Lofty words, perhaps – but if buying a pair of his shoes will last you 20 years, then maybe it’s something we should be taking just as seriously.